JIT Manufacturing Ceding To 3D Printing | Supply Chain Experiencing Disruptive Transition | SDP156
[Podcast] One lesser-mentioned reason for the sustained and worsening supply chain disruption is that manufacturing has entered the “transfer portal” between JIT and 3D printing. In other words, an old technology is being usurped by a new technology. The pandemic hastened the process and the question centered on in this episode is how the baton pass will occur as the race track is quaking.
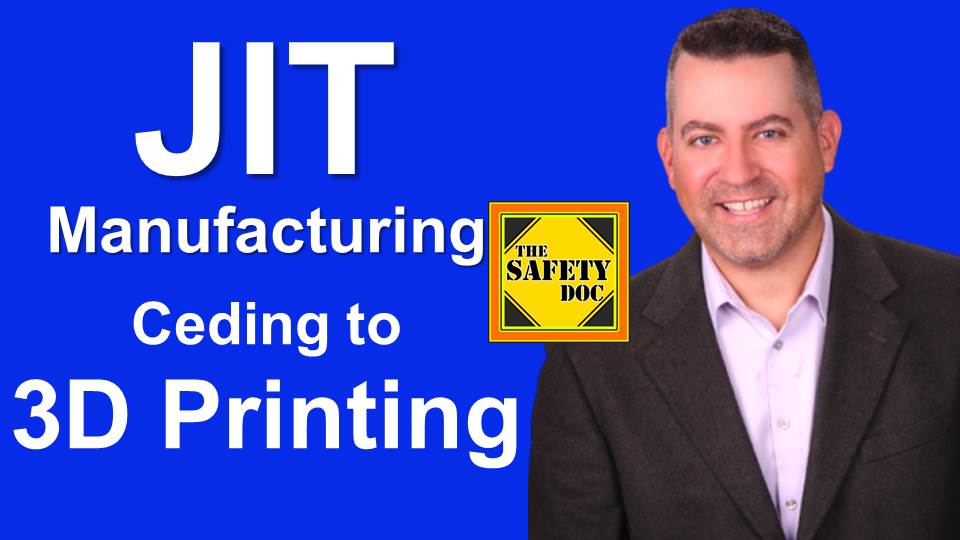
DIRECT LINK to MP3 of this Episode: https://tinyurl.com/SDP156-AUDIO
WAREHOUSE to JIT to 3D PRINTING. In the 1990s, manufacturing experienced an evolution from warehouse manufacturing (or creating excess product and to ship as needed), to Just In Time (JIT) manufacturing – which meant products would skip the warehouse and go directly from the manufacturer to the store / business / consumer. JIT was clunky at first, but as computers improved, RFID to quickly track and improve asset management, and sophisticated transportation logistics, the JIT system was proven, and improving, by the early 2000s.
3D-PRINTED HOUSES GO MAINSTREAM. (Yahoo News’ Joann Muller, Monday, October 25, 2021) Doc shares a story about 3D-printed cement houses. Instead of conventional materials like steel, aluminum and lumber, 3D-printed structures are built by a robot squeezing a cement mixture out of a nozzle, layer upon layer, like a soft swirl ice cream cone. It’s the same additive manufacturing process used to make everything from dental implants to airplane parts — just on a much, much larger scale. Texas-based ICON has delivered two dozen 3D-printed homes in the US and Mexico and has raised $207 million to expand. The homes are printed on-site. While something as disruptive as 3D printed houses seems far-fetched, Doc noted that from 1908 to 1940, you could choose from over 400 styles of homes to purchase through Sears, Roebuck and Co. mail-order catalog.
HOW 3D-PRINTED FOOD COULD CHANGE THE WAY WE COOK AND EAT. General Electric’s GE Additive Manufacturing branch released a report in 2020 describing 3D-printing of food as entering mainstream testing. “At one gourmet restaurant in the United Kingdom, everyone is eating 3D-printed food because that is all that is served. The enterprising entrepreneurs at London’s Food Ink decided to push additive manufacturing to its logical extreme. Everything is 3D printed, including the utensils, plates, tables and chairs. At Miramar, a gourmet restaurant in Spain, food printers take on more mundane tasks, freeing chefs to better focus on their creative cuisine.”
BENEFITS OF 3D PRINTING (Statsys.com) (1) Advance time-to-market turnaround; (2) Save on tooling costs with on-demand 3D printing; (3) Reduce waste with additive manufacturing; (4) Save weight with complex part designs; (5) Eliminate shipping of finished products, along with packaging.
ISSUES WITH 3D PRINTING (1) Need for raw materials – you won’t be able to harvest from your backyard; (2) Intellectual property enforcement – while some open source and public domain, it’s most likely 3D printers will have a subscription service like Amazon; (3) Unclear as to how 3D printed items will be recycled; (4) What is liability if you 3D print something that fails – like a part for your car; (5) Ransomware and hackability. What prevents 3D food printers from being corrupted?
This is episode 156 of The Safety Doc Podcast recorded on 10-15-2021 and published on 10-26-2021.
FOLLOW
- Watch this episode on “The Safety Doc” YouTube channel https://tinyurl.com/SDP156-VIDEO
- Listen to this episode on PodBean MP3 https://tinyurl.com/SDP156-AUDIO
- Apple Podcasts http://tinyurl.com/SafetyDocApplePodcasts
- SAFETY DOC WEBSITE & BLOG safetyphd.com
- Follow David & The Safety Doc Podcast on Twitter @SafetyPhD
- Email Dr. Perrodin thesafetydoc@gmail.com
Purchase Dr. Perrodin’s book: Schools of Errors – Rethinking School Safety in America





